AS/RS Systems
Maximizing Efficiency with Automated Storage Technology
Efficient inventory management is essential for success. Automated Storage and Retrieval Systems (AS/RS) help warehouses move and store products more efficiently while taking up less space. These automated systems handle the repetitive work of storing and retrieving inventory, which reduces manual labor needs and prevents costly mistakes. While traditional storage methods remain valuable, AS/RS technology offers transformative capabilities for operations facing space constraints, labor challenges, and increasing throughput demands. Prestige provides AS/RS solutions that work with your existing warehouse setup to make daily operations smoother and more reliable.
Our AS/RS System Offerings
AS/RS systems use automation to help warehouses, distribution centers, and manufacturing plants store and retrieve products more efficiently. Prestige offers a range of automated storage solutions that can be tailored to meet your facility's specific requirements:
AS/RS Cranes (Racking Crane Systems): Also known as crane-based AS/RS, these systems automate pallet storage and retrieval within high-bay racking using stacker cranes that move horizontally and vertically along dedicated aisles. Controlled by a Warehouse Management System (WMS), they offer fast, accurate handling of various pallet sizes while maintaining real-time inventory tracking. AS/RS Cranes are Ideal for facilities with limited floor space but significant vertical clearance, racking crane systems reduce forklift traffic, improve safety, and ensure consistent performance across all shifts. Their precise, computerized operation enhances inventory accuracy and optimizes storage density in large-scale warehousing environments.
Vertical Lift Modules: VLMs maximize vertical space utilization by storing items in stacked trays that are automatically delivered to ergonomic access points. These systems provide high-density storage in a compact footprint. VLMs improve picking accuracy while reducing labor requirements and ergonomic strain, offering significant space savings compared to traditional shelving. The enclosed design protects inventory from dust, light, and unauthorized access while presenting items at an optimal working height for operators. Vertical Lift Modules can be installed as standalone units or integrated into picking systems for enhanced efficiency.
Pallet Shuttle Systems: These high density automated storage solutions are designed for rapid pallet movement in deep-lane storage configurations. Pallet shuttle systems provide efficient LIFO or FIFO inventory management while maximizing storage density. They reduce aisle space requirements and minimize forklift travel distances, improving throughput in high-volume operations. The automated guided vehicles operate within the racking structure, moving pallets to and from designated positions without requiring forklift access to each storage location. This design creates highly efficient storage blocks ideal for operations handling multiple pallets of the same product.
Horizontal Carousels: Designed for efficient automated storage and retrieval of smaller items, horizontal carousels rotate shelving units horizontally to deliver products to operators. These systems enhance picking speed and accuracy while reducing labor requirements. Horizontal carousels optimize floor space utilization and integrate with inventory management systems. Multiple units can be arranged in pods with integrated workstations, allowing operators to process orders from several carousels simultaneously. The rotational design minimizes walking distances and search time, dramatically improving picking productivity in high-SKU environments.
Mobile Racking Systems: These dynamic storage solutions combine the space efficiency of high density storage with the accessibility of selective racking. Mobile racking systems have traditional racking systems mounted on motorized bases that move along floor-embedded rails. By eliminating permanent aisles between each rack row, these systems can increase storage capacity substantially while still providing access to any pallet position as needed. When integrated with AS/RS technology, mobile racking creates an exceptionally efficient storage environment that adapts to changing inventory requirements and optimizes both horizontal and vertical space utilization.
Unlock the potential of your storage space – Contact our team for a free consultation!
The Advantages of AS/RS Systems
AS/RS systems do more than just store products – they transform how entire warehouse operations function. These automated solutions offer significant advantages that help businesses meet modern logistics challenges. Key benefits that make AS/RS systems a compelling choice for optimizing warehouse operations include:
- Store More in Less Space: AS/RS systems take advantage of building height, letting you store more products without expanding your footprint. Vertical lift modules and racking systems help maximize every cubic foot of space, reducing the need for facility expansion. These systems significantly reduce the required floor space compared to conventional storage methods by utilizing narrow aisles and vertical space that would otherwise go unused. This space optimization allows businesses to delay costly facility expansions or relocations while accommodating inventory growth.
- Fewer Picking Mistakes: When workers search for products manually, errors occur. AS/RS systems ensure the right product is picked every time, improving customer satisfaction and reducing costly returns or shipping errors. The barcode scanning and location tracking features built into these systems virtually eliminate human picking errors and provide real-time inventory visibility across the operation. This precision improves order accuracy rates and enhances customer confidence in your fulfillment capabilities.
- Lower Operating Costs: By handling repetitive storage and retrieval tasks automatically, facilities need fewer forklifts and operators. This results in reduced labor costs, lower equipment maintenance expenses, and improved energy efficiency. AS/RS systems also minimize product damage from improper handling, reduce inventory shrinkage, and decrease utility costs through optimized lighting and climate control in fully automated storage areas. The operational savings compound over time, delivering consistent return on investment throughout the system’s lifespan.
More Advantages of AS/RS Systems
- Room to Grow: AS/RS solutions adapt as business grows, allowing facilities to start with needed capacity and expand later. Modular designs enable phased implementation and scaling without replacing existing systems. This flexibility lets businesses invest incrementally while still planning for long-term needs. AS/RS systems can also accommodate seasonal fluctuations by easily adjusting to changing throughput requirements and inventory levels, providing operational resilience during peak periods.
- Safer Workplace: Automated systems handle dangerous tasks like reaching tall storage locations or moving heavy pallets. This creates a safer working environment with reduced risk of falls, strains, and forklift accidents. The improved ergonomics of AS/RS picking stations minimize repetitive motion injuries and reduce employee fatigue. Work areas become more organized with less congestion from material handling equipment, further enhancing safety while potentially lowering workers’ compensation costs and improving employee retention.
- Improved Inventory Control: AS/RS systems maintain perpetual inventory counts through automated tracking of every product movement. This real-time visibility eliminates the need for frequent physical inventory counts and provides accurate stock levels at all times. The system can automatically prioritize product rotation based on expiration dates or first-in-first-out requirements, reducing waste and ensuring product freshness for time-sensitive goods.
- Enhanced Throughput Capacity: Modern AS/RS solutions dramatically increase the speed and volume of order processing. With rapid retrieval times and simultaneous operations across multiple picking stations, these systems can handle surges in order volume without staffing increases. This scalable throughput is particularly valuable for e-commerce operations and distribution centers facing unpredictable demand patterns or rapid growth.
Challenges & Considerations
While AS/RS systems offer numerous benefits, they also present considerations that warehouses should evaluate when planning implementation. By carefully considering these factors and working with experienced system integrators, warehouses can successfully navigate the challenges of AS/RS implementation while capitalizing on the significant advantages these systems offer for modern distribution operations.
Initial Investment
Automated systems cost more upfront than traditional storage, but long-term savings from efficiency and reduced labor often offset this. Evaluating total cost of ownership gives a clearer picture of long-term.
System Integration
AS/RS must integrate with your warehouse systems. Legacy software can cause issues if not addressed early. Assessing compatibility and working with experienced vendors helps avoid delays.
Implementation Timeline
AS/RS setup takes longer than traditional systems. A phased rollout reduces disruption, and clear timelines covering delivery, setup, and training help maintain business continuity.
Technical Expertise
AS/RS requires specialized knowledge. Training your team for routine maintenance and partnering with service providers ensures smooth operation and faster issue resolution.
Space Planning
AS/RS systems have specific structural needs like ceiling height, floor levelness, and weight limits. Site assessments help plan for any required facility changes.
Operational Adaptability
Automated systems work best with standard items but may need customization for odd sizes or handling. Planning for exceptions early allows smoother operations.
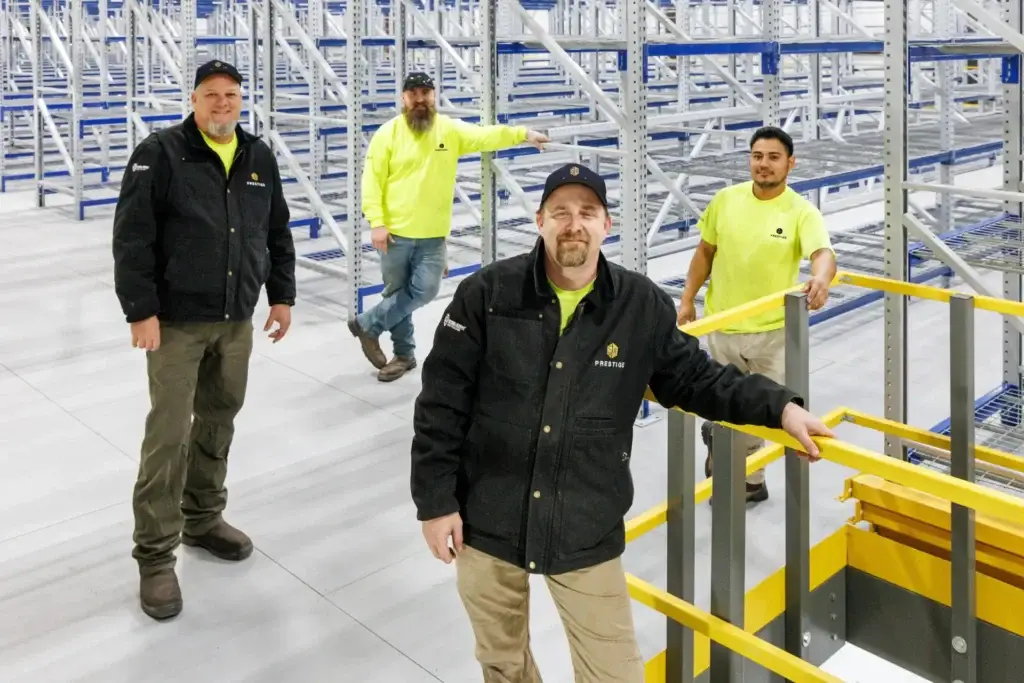
Behind the Automation: The Team Driving Your Storage Success
At Prestige, we are passionate about revolutionizing warehouse storage and material handling solutions. We have been at the forefront of providing innovative, efficient, and customized storage solutions for businesses across various industries.
Our team of experts brings extensive experience in automated systems, traditional storage methods, and space transformation. We pride ourselves on blending cutting-edge technology with practical applications, offering our clients the best solutions for their specific operational needs.
Whether you’re looking to implement advanced AS/RS technology or enhance your existing storage systems, Prestige is your trusted partner. We’re not just about selling products; we’re about providing solutions that address your unique challenges and help your business thrive.
Join the many satisfied clients who have experienced the Prestige difference. Let us help you unlock the full potential of your warehouse space and revolutionize your supply chain with the right AS/RS solution.
FAQ
Commonly Asked Questions
What's the difference between various types of AS/RS systems?
AS/RS systems vary based on storage needs and operational requirements. Vertical lift modules work best for storing small to medium-sized parts in a compact footprint, optimizing vertical space while providing ergonomic access. Racking crane systems handle full pallets in high-bay warehouses, offering efficient storage and retrieval in facilities with significant height. Pallet shuttle systems provide high-density storage for operations with deep lanes and similar product types. Horizontal carousels offer rapid access to small items in a space-efficient configuration. Each system serves different purposes based on inventory characteristics, throughput requirements, and facility constraints.
How do AS/RS systems increase storage density?
AS/RS systems maximize space utilization through several mechanisms. They operate in narrower aisles than traditional forklift-accessible racking, reducing the space needed for equipment movement. These systems effectively use vertical space up to the ceiling, often doubling or tripling storage capacity compared to conventional methods. AS/RS enables deeper storage lanes that would be impractical with manual retrieval methods, particularly in pallet shuttle systems. By optimizing both horizontal and vertical dimensions, AS/RS increases storage density compared to traditional storage methods while maintaining or improving inventory accessibility.
Can AS/RS systems integrate with our existing warehouse management system?
Yes, modern AS/RS solutions are designed with integration capabilities for existing warehouse management systems. Prestige’s implementation team ensures proper communication between automated equipment and your current WMS through standard protocols and custom interfaces. This integration maintains inventory accuracy while enabling fully automated storage and retrieval operations to function with order fulfillment processes. While some legacy systems may require additional middleware or upgrades, most contemporary WMS platforms readily connect with AS/RS equipment. Our experts evaluate your current systems during the planning phase to identify and address any potential integration challenges before implementation.