Integrating a VLM
In today’s fast-paced warehouse and distribution environment, maximizing storage capacity, improving retrieval speed, and optimizing space are crucial to maintaining competitive operations. A Vertical Lift Module (VLM) is a cutting-edge solution that allows businesses to make the most of their building clearance while streamlining inventory management. But how do you successfully integrate a VLM into your facility? This guide will walk you through the essential steps for a smooth and effective VLM integration.
What is a Vertical Lift Module?
Before diving into integration strategies, it’s important to understand what a Vertical Lift Module is and how it works. A VLM is an automated storage and retrieval system (AS/RS) designed to maximize vertical space in warehouses, manufacturing plants, and distribution centers. It consists of two columns of trays on the front and backside of the machine and a central extractor, or elevator, that retrieves and delivers items based on commands from an integrated software system.
With its compact design, the VLM is ideal for operations with limited floor space but significant vertical clearance. It can significantly reduce retrieval times, improve picking accuracy, and decrease labor costs—all of which make it a prime candidate for modern storage optimization.
Step 1: Assess Your Operational Needs
The first step towards integrating a VLM is to assess your existing storage systems and operational needs. Are you experiencing inefficiencies due to lack of space or poor inventory tracking? Are there repetitive manual processes that could be automated? A comprehensive review of your current setup will help you determine how a VLM can improve your processes and what specifications you should be considering.
Questions to ask during this assessment include:
- What types of items do you store, and how frequently are they accessed?
- How much vertical space is available in your facility?
- What are your retrieval speed requirements, and can a VLM meet those needs?
A clear understanding of your specific challenges will guide you in selecting the right VLM model and features.
Step 2: Select the Right VLM
VLMs come in many different size configurations, so selecting the right one for your operation is essential.
Several factors should be considered:
- Storage capacity: How many items or SKUs will be stored in the VLM? Make sure the system’s capacity is adequate for current and future inventory.
- Tray customization: VLM trays can be customized to hold different types and sizes of products. Consider how diverse your inventory is and whether you need flexible tray configurations.
- Picking speed: How quickly does the system retrieve items? Some VLMs are optimized for speed, while others prioritize capacity. Choose a model that balances these factors based on your operation’s needs.
- Operations Process: Ensure you have considered the different methods for operation, and have an understanding of which will likely work best for your facility, whether that be call by tray, call by part number, or call by order number. If you have an existing Warehouse Management System (WMS) or Enterprise Resource Planning (ERP) system, consider what will be necessary to integrate with a VLM. This is crucial for seamless inventory management.
At this stage, it’s also worth consulting with a supplier or integrator who specializes in VLM systems to get recommendations tailored to your unique needs. As a certified Modula dealer, our in-house team at Prestige can help guide you through selecting the right Modula VLM model and provide expert installation and support to ensure you get the most out of your system.
Step 3: Design the Layout and Plan the Workflow
Once you’ve selected the appropriate VLM, the next step is to plan its physical integration into your warehouse. Once you’ve selected the appropriate VLM, the next step is to plan its physical integration into your facility. VLMs utilize vertical space but require strategic placement within your warehouse layout to maximize efficiency.
Key considerations include:
- Access points: Make sure that the VLM is positioned in an area with easy access for operators. Consider its proximity to other equipment, loading docks, or high-traffic areas to ensure a smooth workflow.
- Ergonomics: Since VLMs are designed to deliver items directly to the operator at an ergonomic height, make sure the surrounding area allows for efficient operator movement, including space for loading/unloading items safely and comfortably.
- Buffer zones: You may need to allocate buffer zones around the VLM for items that are in transit or temporarily stored before being loaded into the system.
In some cases, it’s possible to position the VLM next to a mezzanine. VLMs can have three operator bays per tower, and those bays can either be positioned at the floor level or at an elevated level to accommodate multi-level structures. This flexibility allows you to optimize space and streamline workflows based on your facility’s layout and needs.
When planning the VLM’s placement, think about the overall flow of materials in your facility. The goal is to minimize unnecessary travel time and ensure a smooth, efficient process for both inbound and outbound inventory. Lastly, when it comes to machine placement, always plan for future expansion, whether that be additional units or other storage systems.
Step 4: Integrate VLM with Software Systems
One of the key advantages of a VLM is its integration with modern inventory management and WMS systems. A properly integrated VLM allows for real-time tracking of inventory, automatic replenishment, and improved picking accuracy.
Our VLMs come with proprietary software that can either function as a standalone system or connect with other enterprise resource planning (ERP) or WMS platforms. If you’re using a pre-existing WMS, we can work with your IT team or software provider to integrate VLM technology with your systems. Our team of experts are here to lead you through the software infrastructure requirements to ensure you maximize your investment.
Proper integration ensures:
- Real-time inventory tracking: You’ll know the exact location and quantity of every item, eliminating time-consuming manual inventory counts.
- Seamless order processing: Orders can be routed directly to the VLM, where the system will automatically retrieve the items in the correct sequence.
- Data insights: Integrated systems provide valuable data that can help you optimize the use of your VLM over time, from item placement to replenishment strategies.
Step 5: Professional Installation & Service
Installing a VLM is a specialized process that should only be handled by factory trained professionals. This ensures not only that the system functions properly but also that it complies with all relevant safety regulations. At Prestige, we have the expertise to handle the complete installation of Modula VLMs, ensuring a smooth setup tailored to your facility’s needs. Additionally, our in-house team provides ongoing service and support in the aftermarket to keep your system running at peak efficiency, minimizing downtime and ensuring long-term operational success.
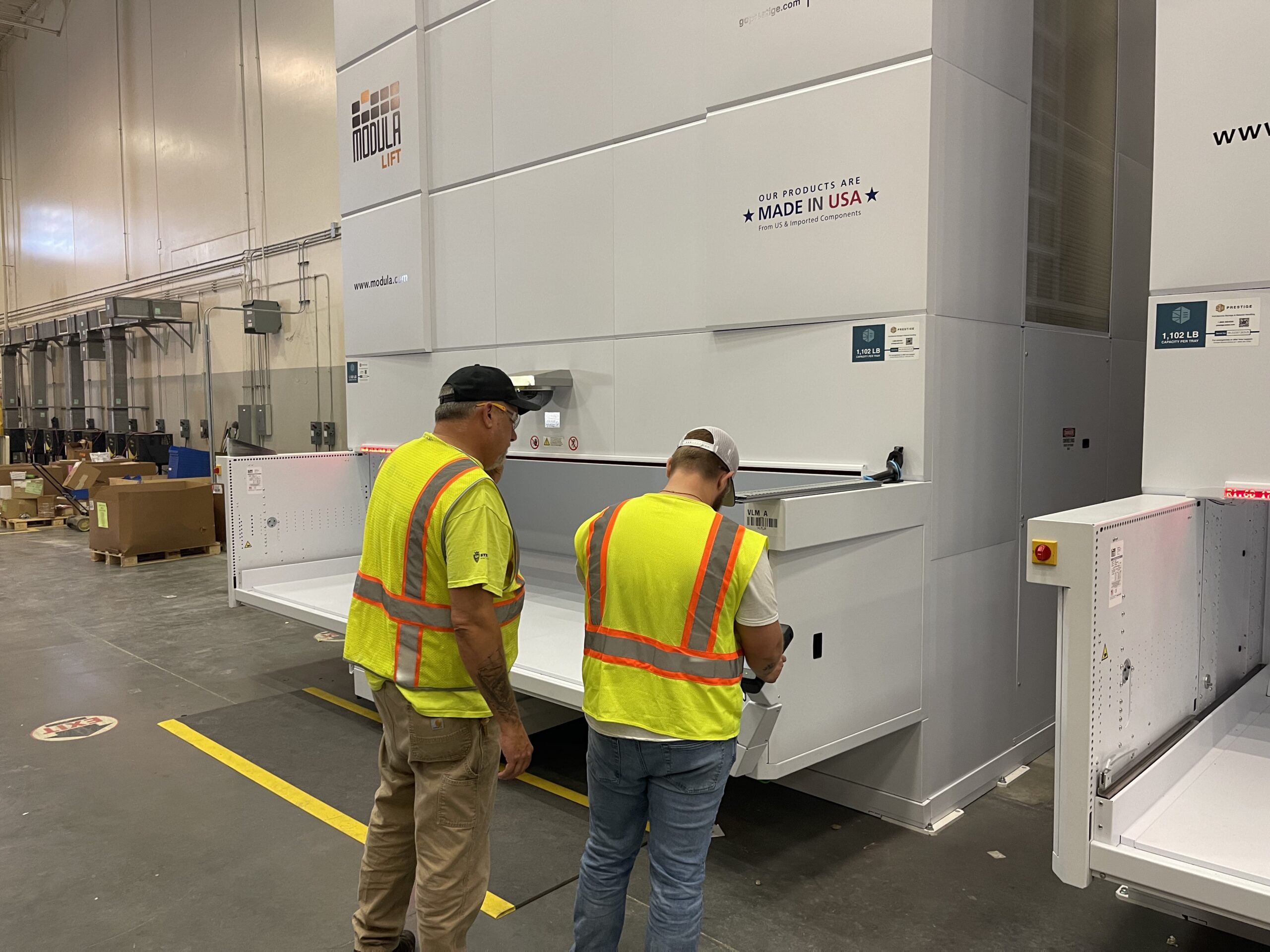
The installation process generally includes:
- Assembly: The physical structure of the VLM is built onsite, with attention paid to elevator levelness and mechanical functionality.
- Software setup: The control software is installed and integrated with your existing systems.
- Testing: Once installed, the VLM undergoes rigorous testing to ensure it meets all performance specifications, including tray movement, retrieval speed, and software integration.
Step 6: Staff Training and Safety
The final step in your VLM integration process is training your staff. While VLMs are designed to be user-friendly, comprehensive training ensures that operators can handle the system efficiently and safely, reducing the likelihood of operational errors.
Training should cover:
- Basic operation: How to input orders, retrieve items, and manage the system’s interface.
- Safety protocols: Understanding load capacities, safety interlocks, and what to do in case of a system malfunction or emergency stop.
- Routine maintenance: Basic troubleshooting and maintenance tasks to keep the system running smoothly, minimizing the risk of downtime.
Properly trained staff significantly reduce the risk of errors that could lead to costly maintenance issues or downtime. By ensuring that operators are knowledgeable and confident in using the VLM, you’ll minimize the need for external support. In addition to initial training, ongoing sessions are recommended, especially if your facility undergoes operational changes or the VLM is upgraded with new features. This approach keeps your team updated and reduces the chances of preventable issues.
Conclusion
A well-integrated Vertical Lift Module can be a game-changer for your warehouse or distribution center, significantly improving storage efficiency, picking accuracy, and operational workflow. By carefully planning the integration process—from assessing your needs to installation and training—you can ensure that your VLM delivers long-term value and enhances your overall operational efficiency.
At Prestige, we are a certified Modula dealer, and our full-service team is ready to assist you at every step of the process. From selecting the right Modula VLM for your facility to professional installation and ongoing maintenance, we have the expertise to help you maximize your investment in vertical lift technology. Reach out today to learn more about how we can streamline your operations with Modula’s cutting-edge solutions.