Lift Tables & Material Handling Solutions
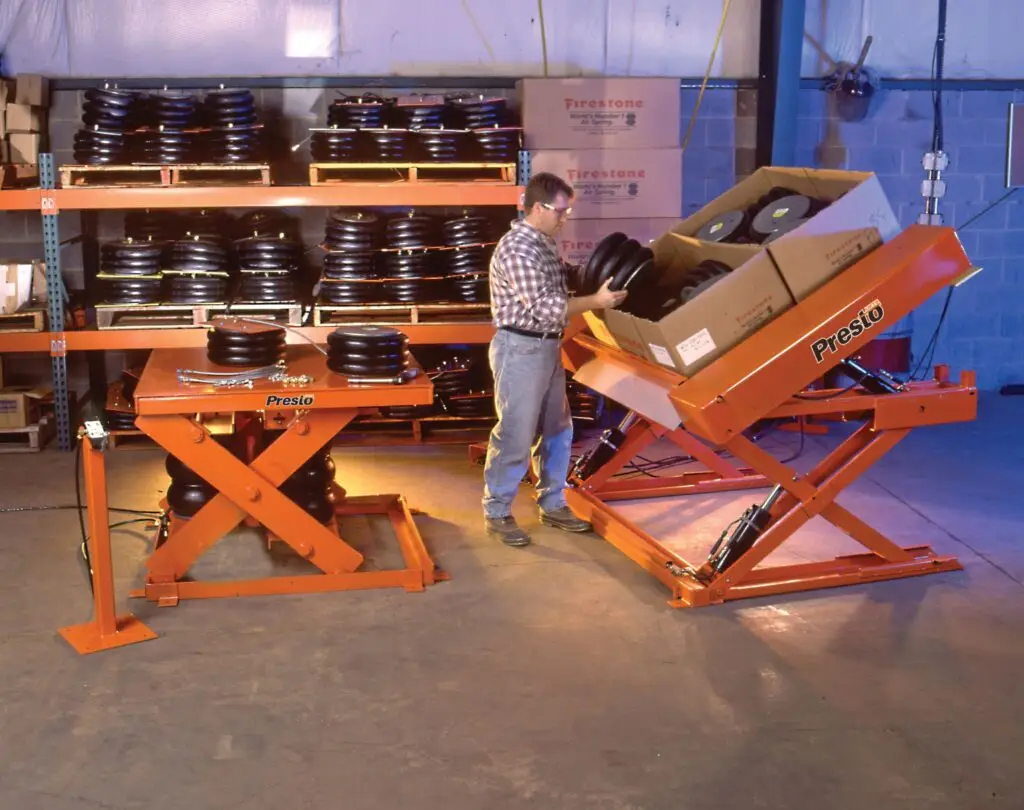
Maximizing Efficiency with Material Handling
In demanding industrial environments, operational efficiency and productivity are paramount to success. Lift tables provide essential material handling capabilities in warehouse and manufacturing settings. These versatile platforms enhance productivity through controlled vertical movement of materials while reducing worker strain. From standard scissor lift tables to specialized configurations, lift tables deliver measurable improvements in operational performance. Prestige offers lift table solutions that transform material handling operations and boost workplace productivity.
Key Types of Lift Tables
Different lift table configurations address specific warehouse and manufacturing needs. Prestige offers a range of lift table solutions that can be tailored to meet your operation’s unique requirements:
Scissor Lift Tables
One of the most common lift tables, scissor lift tables deliver reliable vertical movement through proven hydraulic or pneumatic systems. Their design handles diverse loads consistently across multiple shifts, making them ideal for repetitive lifting operations that demand dependable performance.
Tilt Lift tables
Built for operator comfort and efficiency, tilt lift tables combine lifting power with adjustable positioning. The tilting function reduces physical strain in assembly and packaging operations by minimizing reaching and bending. Operators gain easier access to containers and boxes, boosting both productivity and ergonomic efficiency.
Portable Lift Tables
Flexibility meets functionality with portable lift tables equipped with heavy-duty casters. These mobile units adapt to changing workspace needs, supporting dynamic floor layouts and temporary material handling requirements. Quick repositioning capabilities ensure your operation maintains peak efficiency even as demands shifts.
Unlock the potential of your storage space – Contact our team for a free consultation!
The Advantages of Lift Tables
Lift tables offer significant advantages for industrial operations of all sizes. These versatile solutions balance efficiency, productivity, and ergonomics, which many businesses find invaluable. Some key benefits that make lift tables a compelling choice for optimizing warehouse operations include:
- Improved Ergonomics: By positioning materials at optimal working heights, lift tables reduce physical strain and improve employee comfort.
- Increased Productivity: Proper material positioning speeds up handling processes and reduces fatigue-related slowdowns.
- Versatility: Lift tables adapt to various applications across different departments and operational needs.
- Durability: Industrial-grade construction ensures reliable performance in demanding environments.
- Operational Efficiency: Lift tables reduce manual lifting and awkward movements, streamlining workflows and reducing operational costs.
Challenges & Considerations
While lift tables offer numerous benefits, understanding potential challenges helps ensure successful implementation:
- Space Requirements: Some lift table configurations require adequate floor space for optimal operation and access. Planning for proper clearance around the equipment ensures operators can effectively access materials and controls without obstruction. Larger platforms or specialized configurations may need additional surrounding space for optimal functionality. Consider both the footprint of the equipment itself and the necessary operational space when planning installations. Evaluating workspace layouts in advance helps identify potential constraints and opportunities for efficient equipment placement within your facility structure.
- Power Access: Hydraulic systems typically require electrical power sources for operation. Planning for power availability and distribution affects equipment placement and installation requirements. Some applications may benefit from battery-powered options when fixed power sources are impractical. Understanding voltage requirements and circuit capacities ensures compatible infrastructure for new equipment. Backup power considerations may also be relevant for operations where continuous availability is critical during power interruptions.
- Maintenance Needs: Regular maintenance ensures optimal performance and extends equipment lifespan. Understanding maintenance schedules and requirements helps budget for ongoing operational costs. Establishing preventive maintenance programs supports consistent equipment reliability and performance. Access to qualified service technicians affects long-term operational planning and support resources. Proper maintenance documentation and scheduling systems help track equipment history and anticipate future service needs before they impact operations.
- Load Distribution: Proper load placement and weight distribution are necessary for reliable operation. Training operators in correct loading techniques prevents equipment damage and operational disruptions. Understanding weight capacity limitations and center of gravity considerations ensures effective material handling. Different materials and container types may require specific placement guidelines for optimal stability. Establishing clear loading protocols supports consistent operational practices across multiple shifts and operators.
- Environmental Factors: Operating conditions like temperature and moisture may affect lift table selection. Special configurations are available for wash-down environments or corrosive settings. Temperature extremes in cold storage or hot manufacturing areas require appropriate equipment specifications. Understanding environmental challenges helps select components and finishes that will perform reliably in your specific conditions. Indoor versus outdoor applications present different durability requirements and weather resistance considerations that impact equipment selection.
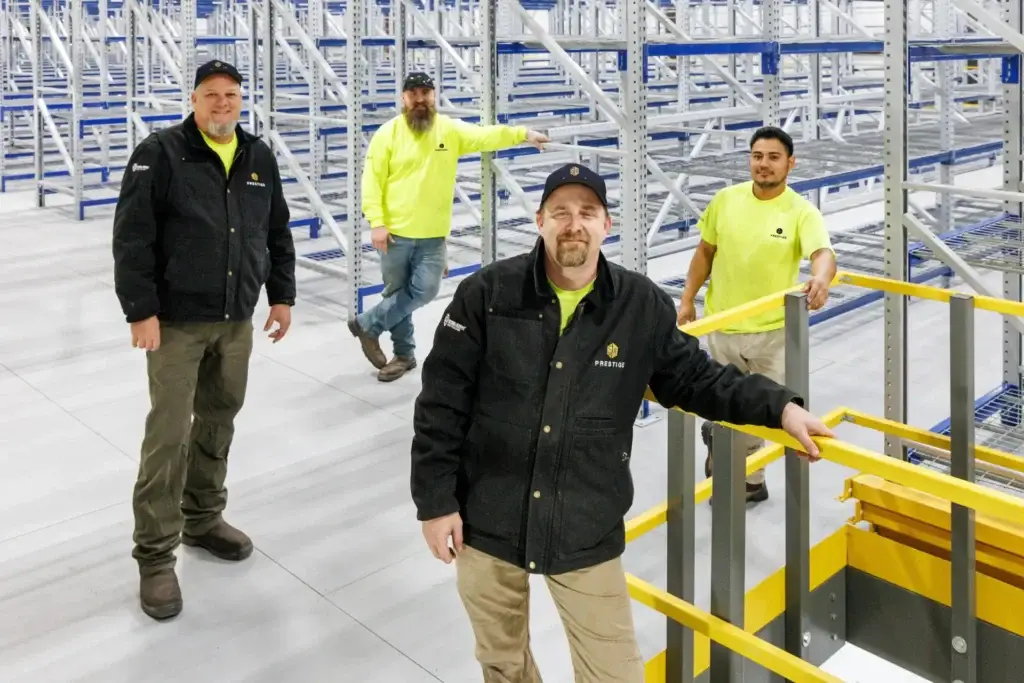
Behind the Equipment: The Team Driving Your Material Handling Success
At Prestige, we are passionate about revolutionizing warehouse storage and material handling solutions. We maintain extensive inventory at our Chattanooga, TN facility, allowing us to reduce project lead times and provide competitive rates while ensuring consistent product availability for our clients.
Our team of experts brings extensive experience in material handling equipment, space transformation, and automated systems. We pride ourselves on blending practical solutions with innovative approaches, offering our clients the best of both worlds.
Whether you’re looking to optimize warehouse efficiency or completely transform your material handling processes, Prestige is your trusted partner. We’re not just about selling products; we’re about providing solutions that address your unique challenges and help your business thrive.
Join the many satisfied clients who have experienced the Prestige difference. Let us help you unlock the full potential of your warehouse operations and revolutionize your material handling processes.
FAQ
Commonly Asked Questions
What is the difference between standard and low profile scissor lift tables?
Low profile scissor lift tables offer a reduced collapsed height, making them ideal for applications where minimal entry height is crucial. These units provide easier pallet jack access and enhanced ergonomics for ground-level loading, while maintaining lifting capabilities.
What factors should I consider when selecting lift table capacity?
Key considerations include the maximum load weight, frequency of use, type of materials being handled, and environmental conditions. Consider both static and dynamic load requirements, along with any future capacity needs your operation may have.
Can lift tables be customized for specific applications?
Yes, lift tables can be customized with various platform sizes, capacities, and features to meet specific operational requirements. Prestige can help determine the right configuration for your unique application needs.