Warehouse Optimization
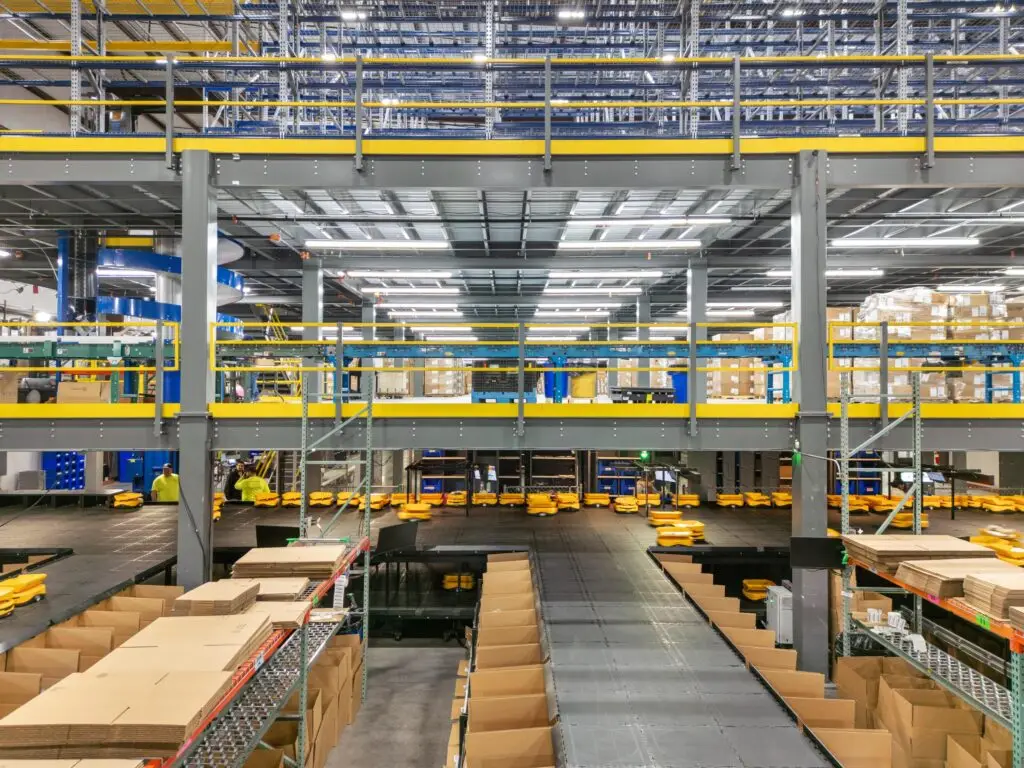
Enhancing Storage & Integrating Automation
Warehouse efficiency directly affects your costs, productivity, and customer satisfaction. If you’re facing space constraints, workflow bottlenecks, or outdated storage methods, a smart optimization strategy can turn inefficiencies into opportunities—reducing costs while improving throughput. From traditional storage solutions like pallet racking and shelving to cutting-edge automated storage systems like Vertical Lift Modules and Pallet Shuttle Systems, we’ll explore strategies to enhance your facility’s productivity and profitability. Optimizing your warehouse means evaluating every process that impacts efficiency—from the moment inventory arrives to final shipment.
While storage solutions are essential, optimization extends to workflow design, equipment utilization, and space management. When key performance indicators (KPIs) are optimized, warehouses experience lower operational costs and improved order fulfillment speeds. Key metrics that indicate optimization opportunities include order accuracy rate, picking efficiency, space utilization, throughput rate, inventory turnover, labor cost per unit shipped, and dock-to-stock time. Monitoring these metrics provides a data-driven foundation for warehouse optimization, allowing for targeted improvements where they’ll deliver maximum impact.
Key Components of Warehouse Optimization Solutions
Warehouse optimization systems form the foundation of efficient operations and space utilization. Prestige offers a range of solutions designed to meet diverse operational needs:
Space Optimization & Transformation: Make better use of your facility with solutions that add space and improve layout efficiency. Mezzanines create usable square footage for storage, offices, or production without expanding your building. Wire partitions and cages define secure zones, while vinyl curtains offer flexible separation for temperature, dust, or noise control. Thoughtful aisle layouts reduce wasted space, and automated systems like VLMs help consolidate inventory and speed up retrieval.
Traditional Storage Systems: Built for accessibility and volume, traditional systems support a wide range of inventory types. Pallet racking offers scalable storage with direct access for manufacturing and distribution. High-density configurations maximize available space for bulk storage and high-SKU operations, while shelving and cabinets improve organization for small parts. These systems are widely used in industries like healthcare, automotive, and foodservice.
Automated Systems: Automated solutions streamline storage and retrieval while saving space. VLMs deliver items to operators quickly and efficiently. Horizontal carousels speed up picking for small, high-turnover items. Pallet shuttle systems handle deep-lane storage with reduced forklift traffic, boosting throughput in demanding warehouse environments.
Unlock the potential of your storage space – Contact our team for a free consultation!
The Advantages of Warehouse Optimization
Warehouse optimization offers significant advantages for facilities of all sizes. These strategic improvements balance operational efficiency, cost reduction, and enhanced capacity, which many businesses find invaluable. Some key benefits that make warehouse optimization a compelling choice include:
- Increased Storage Capacity: Optimized facilities can store significantly more inventory within the same footprint, eliminating the need for facility expansion. By maximizing vertical space utilization, implementing high-density storage systems, and reducing aisle width where appropriate, warehouses can substantially increase storage capacity without expanding their physical footprint.
- Enhanced Productivity: Streamlined workflows and optimized picking processes can substantially increase throughput with the same labor resources. Efficient slotting, optimized pick paths, and inventory placement reduce travel time for warehouse personnel, dramatically improving order fulfillment rates and overall warehouse productivity.
- Improved Accuracy: Well-designed systems and processes reduce errors in picking, packing, and shipping operations. By implementing verification protocols, clear inventory location systems, and proper lighting, warehouses can achieve exceptional accuracy rates, significantly reducing costly returns and improving customer satisfaction.
- Reduced Operating Costs: More efficient space utilization and labor allocation lead to lower costs per unit handled. Optimized warehouses experience considerable reductions in operating costs through decreased labor requirements, lower energy consumption, improved space utilization, and reduced product damage.
- Greater Flexibility: Optimized warehouses can more easily adapt to changing business needs and seasonal fluctuations. Modular storage systems, reconfigurable workstations, and scalable automation allow facilities to quickly adjust to shifting inventory profiles, order patterns, and business requirements without major disruptions.
Challenges & Considerations
While warehouse optimization offers numerous benefits, it also presents some challenges:
- Implementation Disruption: Significant changes to layout or systems may temporarily impact operations during installation. Reconfiguring racking systems, installing automation, or redesigning workflow patterns can create short-term productivity challenges while delivering long-term efficiency gains.
- Investment Requirements: Certain optimization solutions require substantial upfront investment before delivering long-term returns. Advanced technologies and storage systems represent a significant capital expenditure that must be evaluated against projected operational improvements and space utilization benefits.
- Phased Approach: Complete optimization often requires a strategic, phased implementation plan to minimize disruption. Breaking larger projects into manageable segments allows operations to continue while improvements are gradually integrated into the workflow.
- Workforce Adaptation: Staff may need training and time to adjust to new systems and workflow processes. Proper change management strategies help ensure employees embrace new optimization solutions rather than resist unfamiliar procedures and technologies.
By strategically implementing optimization solutions and combining them with effective management techniques, businesses can transform their warehouse operations without unnecessary disruption. Warehouse optimization continues to offer a reliable, adaptable approach to meeting increasing demands for efficiency and throughput in today’s competitive market.
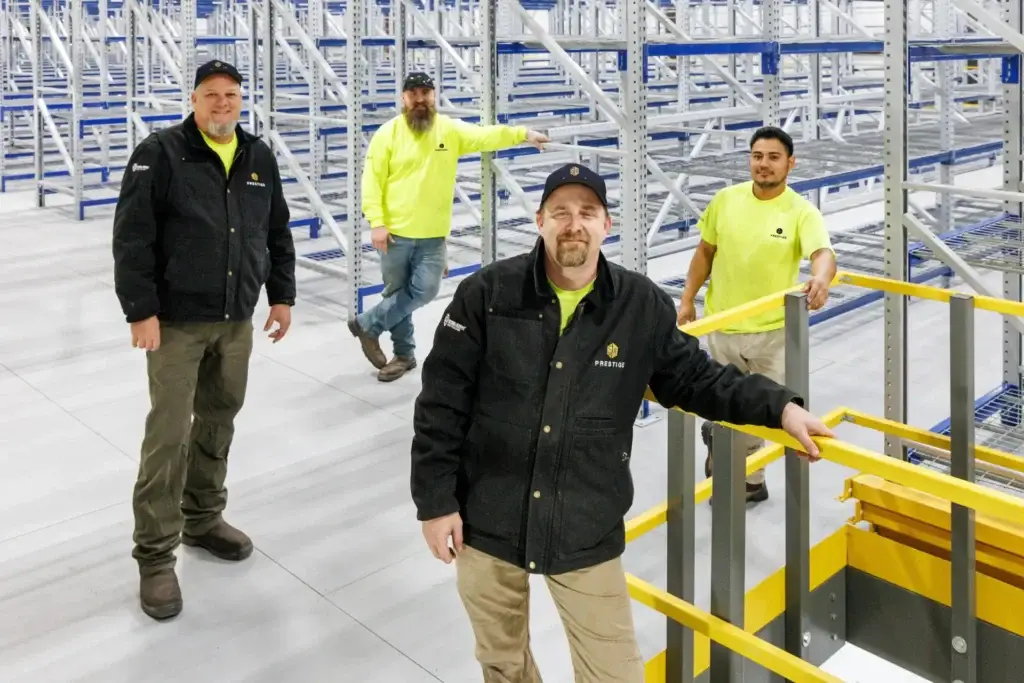
Your Warehouse Optimization Partner
Since 1970, Prestige has led the Southeast in delivering high quality storage and material handling solutions. We analyze your facility’s unique requirements to provide customized solutions that maximize space utilization and operational efficiency.
Our team of warehouse optimizers brings decades of experience in warehouse optimization, space transformation, and automated systems. We pride ourselves on blending proven optimization techniques with cutting-edge technology, offering our clients the best of both worlds.
Whether you’re looking to streamline your existing operations or completely transform your warehouse space, Prestige is your trusted partner. We’re not just about selling products; we’re about providing solutions that address your unique challenges and help your business thrive.
With an extensive inventory of pallet racking material, shelving, warehouse safety products, and advanced storage components, our expert team delivers solutions designed for lasting efficiency gains. Let’s optimize your warehouse for maximum efficiency. Contact us today for a site evaluation and customized solution proposal.
FAQ
Commonly Asked Questions
How can we reduce travel time in our warehouse operations?
Travel time reduction starts with strategic layout planning and optimized pick paths. Implementing batch picking strategies, reorganizing fast-moving items, and utilizing automated storage systems can reduce unnecessary movement throughout your facility. Proper slotting—placing high-velocity items in easily accessible locations—creates significant efficiency gains. When combined with zone picking and proper aisle design, these strategies can dramatically decrease travel distance and time, allowing for more productive use of labor resources.
What strategies improve pick optimization in warehouse operations?
Effective pick optimization combines product placement, efficient pick paths, and appropriate technology integration. Solutions range from basic improvements like zone picking to advanced systems such as vertical lift modules that bring products directly to warehouse operators. Batch picking multiple orders simultaneously can dramatically improve efficiency for smaller items. Voice-directed or light-directed picking systems can further enhance accuracy while reducing training time. The ideal picking strategy depends on your specific product mix, order profiles, and throughput requirements.
How do you maintain accurate inventory levels in an optimized warehouse?
Accurate inventory management relies on systematic cycle counting programs, integrated inventory management systems, and proper training protocols. Regular audits and real-time tracking capabilities ensure inventory accuracy while minimizing disruptions to daily operations. Implementing location-based inventory tracking with proper zone and bin identification creates accountability throughout the warehouse. Combining these approaches with strategic slotting that minimizes similar-looking items being stored together significantly reduces picking errors and inventory discrepancies.