Types of Pallet Racking Systems
In today’s fast-paced business environment, efficient warehouse storage is crucial for optimizing space and improving operational efficiency.
Pallet racking systems are essential for organizing and storing materials in warehouses, distribution centers, and manufacturing facilities. Understanding the different types of pallet racking systems can help you select the best option for your needs. Let’s explore the most common types of pallet racking systems and their benefits.
1. Selective Pallet Racking
Selective pallet racking is the most common, versatile, and economical racking system used in warehouses across various industries. This system is designed to allow direct access to every pallet, which is stored on horizontal beams.
The straightforward structure makes it easy to install and reconfigure according to changing storage needs. Selective pallet rack can be compatible with essentially any type of fork lift, it just requires the appropriate aisle width. This elasticity makes it a popular choice for many warehouses.
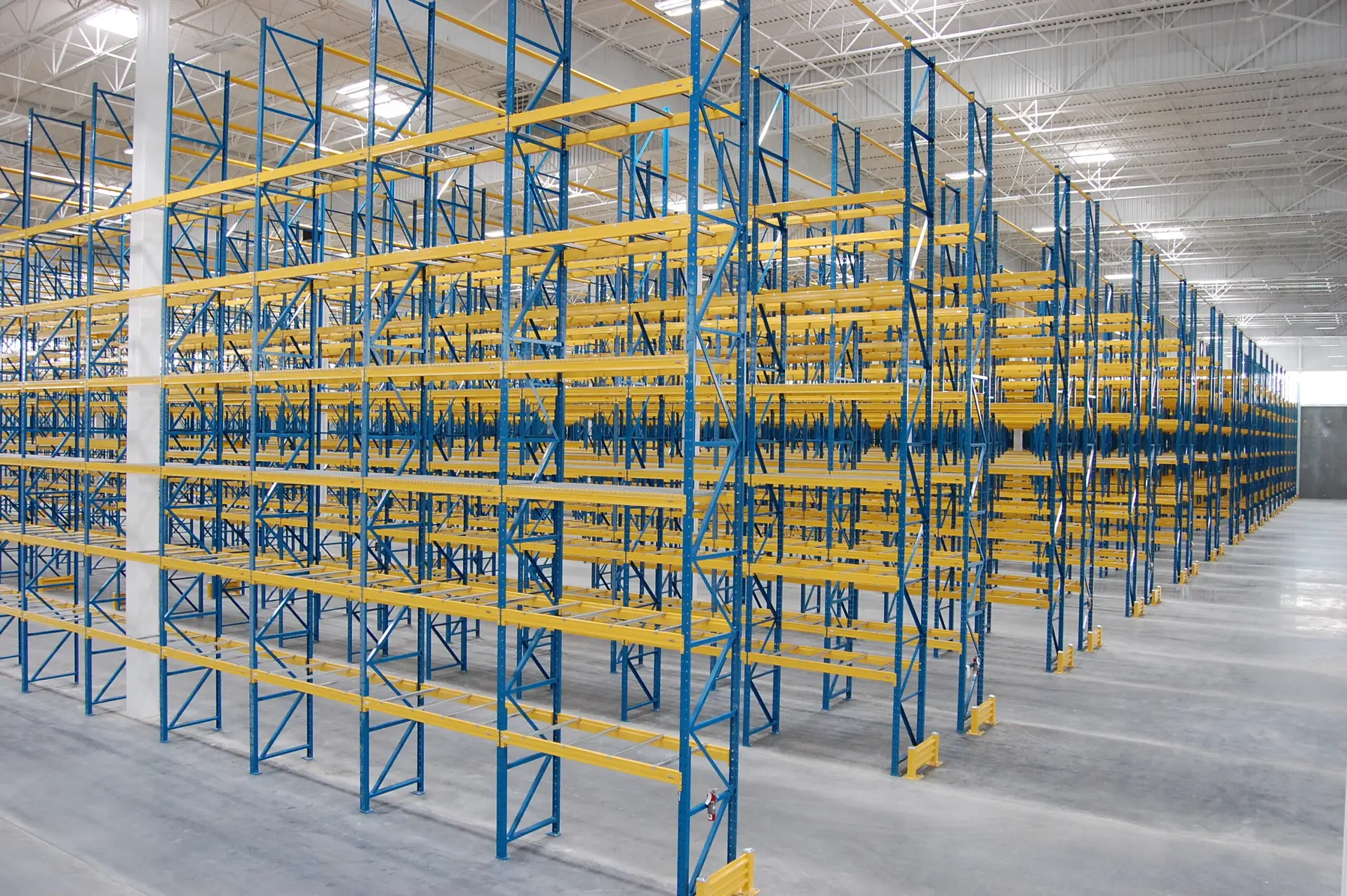
Key Benefits of Selective Racking:
- Easy Access: Direct access to each pallet enhances inventory management and order picking efficiency. This ease of access reduces the time required to retrieve products, leading to faster order fulfillment and improved customer satisfaction.
- Flexibility: Compatible with various pallet sizes and types of material handling equipment. Selective racking can be adjusted to accommodate different product dimensions, making it a highly adaptable solution. Due to its versatile, selective pallet rack is the backbone of many automated storage systems.
- Cost-Effective: Relatively low cost and easy to install. The straightforward design of selective racking makes it a budget-friendly option for businesses looking to optimize their storage solutions without a significant investment.
2. Drive-In and Drive-Through Racking
Drive-in and drive-through racking systems are designed to maximize storage density by minimizing the number of aisles required in a warehouse. These systems are particularly useful for storing large quantities of similar products, such as bulk goods.
Drive-in racking allows forklifts to enter from one side to pick up or deposit pallets, making it suitable for Last-In-First-Out (LIFO) inventory systems. In contrast, drive-through racking enables forklifts to access pallets from both sides, supporting a First-In-First-Out (FIFO) system. This racking type is built to handle high-density storage needs, ensuring optimal use of space and enhancing operational efficiency.
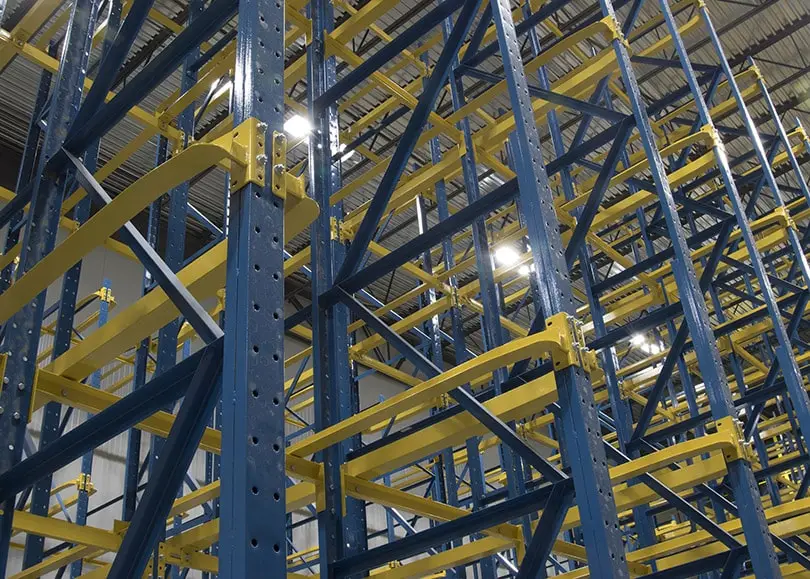
Key Benefits of Drive-In / Drive-Through Racking:
- High Density: Maximizes storage space by reducing the number of aisles. This system is perfect for warehouses with a high volume of similar products, allowing for the efficient use of vertical space. It is critical to optimize the lane depth in drive-in / drive-through racking, as in most applications entire lanes are either loaded or unloaded all at one time.
- Cost Efficiency: Ideal for storing large quantities of homogeneous products. The high-density nature of drive-in and drive-through racking systems makes them a cost-effective solution for bulk storage.
- FIFO and LIFO: Drive-through racking supports First-In-First-Out (FIFO), ensuring that older products are used first, while drive-in racking supports Last-In-First-Out (LIFO), suitable for non-perishable goods.
3. Push-Back Racking
Push-back racking is an advanced storage solution designed for high-density storage environments. It operates on a dynamic system of carts on inclined rails, allowing pallets to be loaded from the front and then pushed back by subsequent pallets.
This type of racking is ideal for warehouses that need to store multiple pallets of the same product while maintaining a relatively high level of accessibility. Push-back racking systems can hold multiple pallets deep, optimizing the use of available space without compromising on access to products. They are particularly beneficial in warehouses where storage density and efficiency are paramount.
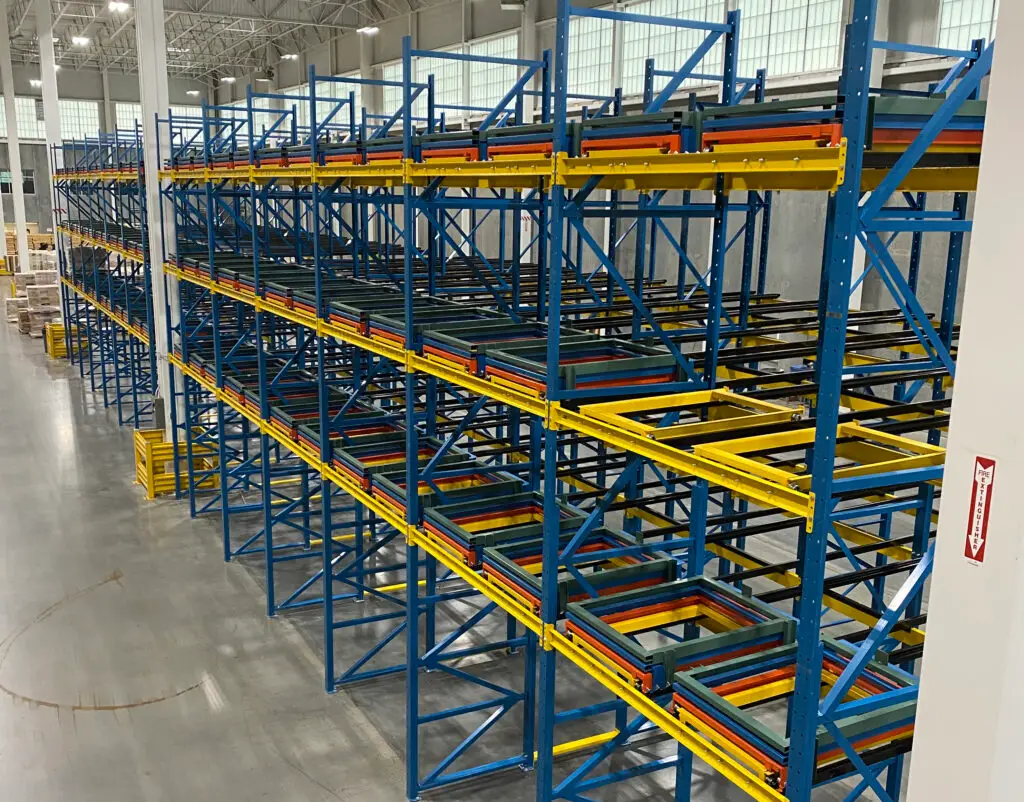
Key Benefits of Push-Back Racking:
- Space Utilization: Increases storage density by storing pallets up to six deep. This makes push-back racking an excellent choice for warehouses needing to maximize space without expanding their footprint.
- Accessibility: Offers better selectivity compared to drive-in racking. While not providing direct access to every pallet, it still allows for a more organized approach to inventory management.
- Efficiency: Allows for efficient use of space without sacrificing access to products. This system is particularly useful in environments where both storage density and accessibility are crucial.
4. Pallet Flow Racking
Pallet flow racking, also known as gravity flow racking, utilizes inclined roller tracks to move pallets from the loading end to the picking end. This system leverages gravity to facilitate the movement of pallets, ensuring a smooth and controlled flow of inventory.
Pallet flow racking is ideal for high-turnover storage environments where maintaining product rotation is essential. This system supports First-In-First-Out (FIFO) inventory management, making it particularly suitable for perishable goods and items with expiration dates.
The design of pallet flow racking maximizes storage density while providing easy access to products, ensuring efficient space utilization and streamlined operations.
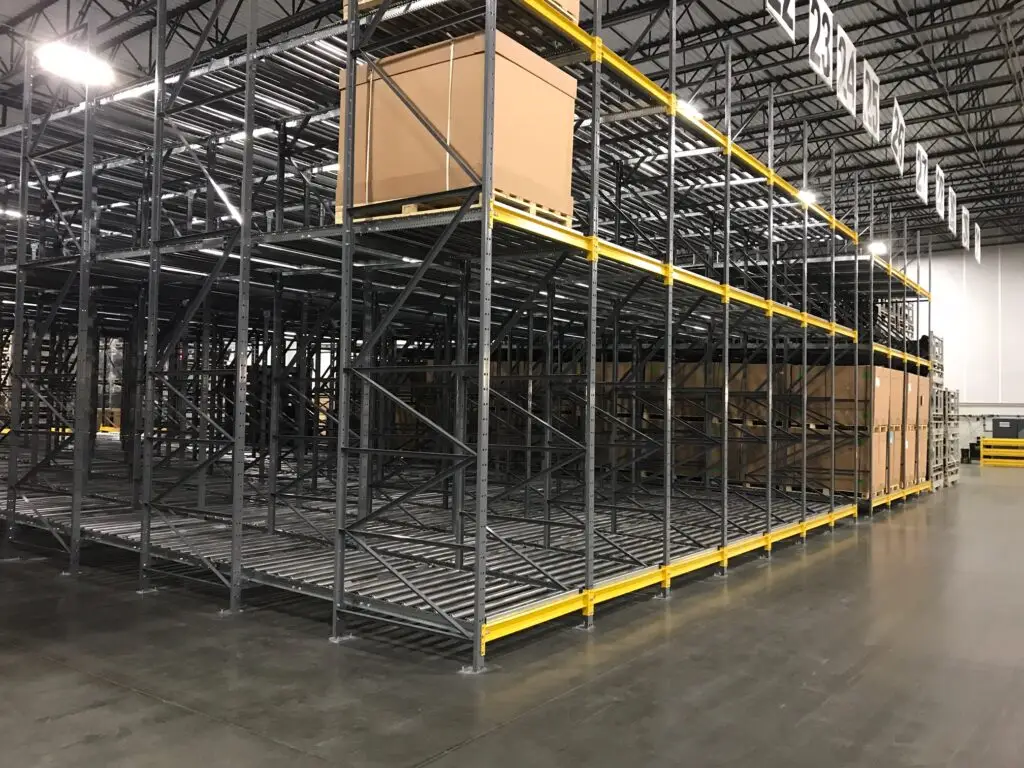
Key Benefits of Pallet Flow Racking:
- FIFO Inventory Management: Ensures products are rotated efficiently. This is particularly important for perishable goods, as it helps maintain product freshness and reduces waste.
- High Density: Provides high-density storage while maintaining easy access to products. Pallet flow racking maximizes storage capacity by utilizing vertical space effectively.
- Reduced Handling: Minimizes the need for forklifts to enter the racking system, reducing handling time and improving overall safety in the warehouse.
5. Mobile Racking
Mobile racking systems are an innovative storage solution designed to maximize storage capacity by eliminating the need for multiple static aisles. These systems are mounted on mobile bases that move along tracks, allowing the racking units to be compacted together when access is not required.
When needed, the aisles can be opened up to provide access to specific pallets. Mobile racking systems are highly efficient and are particularly beneficial in environments where space is at a premium. This type of racking is ideal for businesses looking to significantly increase their storage capacity without expanding their warehouse footprint.
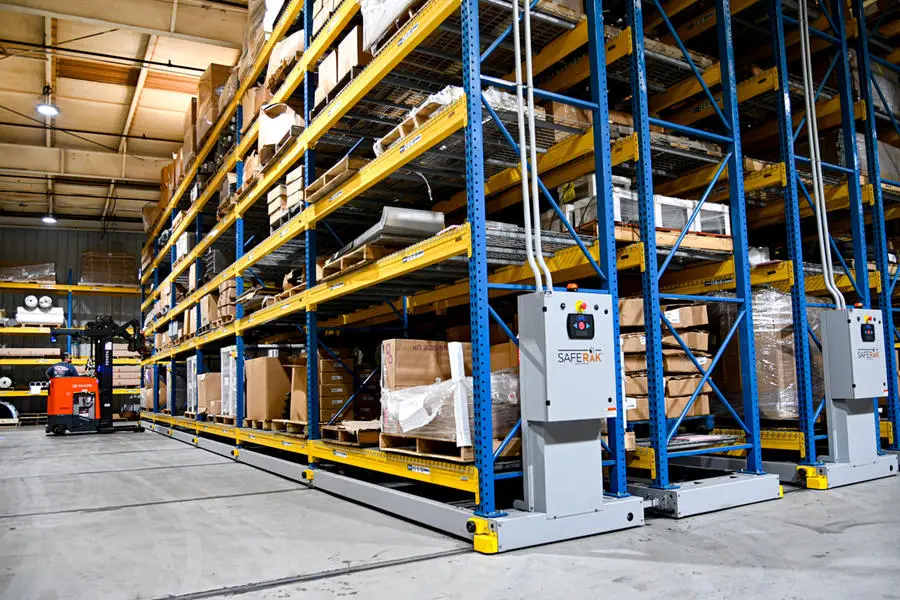
Key Benefits of Mobile Racking:
- High Density: Increases storage capacity by up to 80% compared to static racking. Mobile racking is ideal for warehouses where square footage space is limited, such as cold storage facilities.
- Accessibility: Allows for easy access to any pallet when needed. Despite its high-density design, mobile racking provides excellent accessibility, ensuring efficient inventory management.
- Space Efficiency: The compact design of mobile racking helps businesses make the most of their available space.
6. Pallet Shuttle Systems
Pallet shuttle systems are a cutting-edge automated storage solution designed to maximize warehouse efficiency and storage density. This system utilizes a lithium-ion battery powered shuttle that moves along rails within the racking structure to load and unload pallets.
The pallet shuttle system is ideal for high-density storage environments where large volumes of goods need to be stored and retrieved quickly and accurately. It significantly reduces the need for manual handling, enhancing operational efficiency and safety.
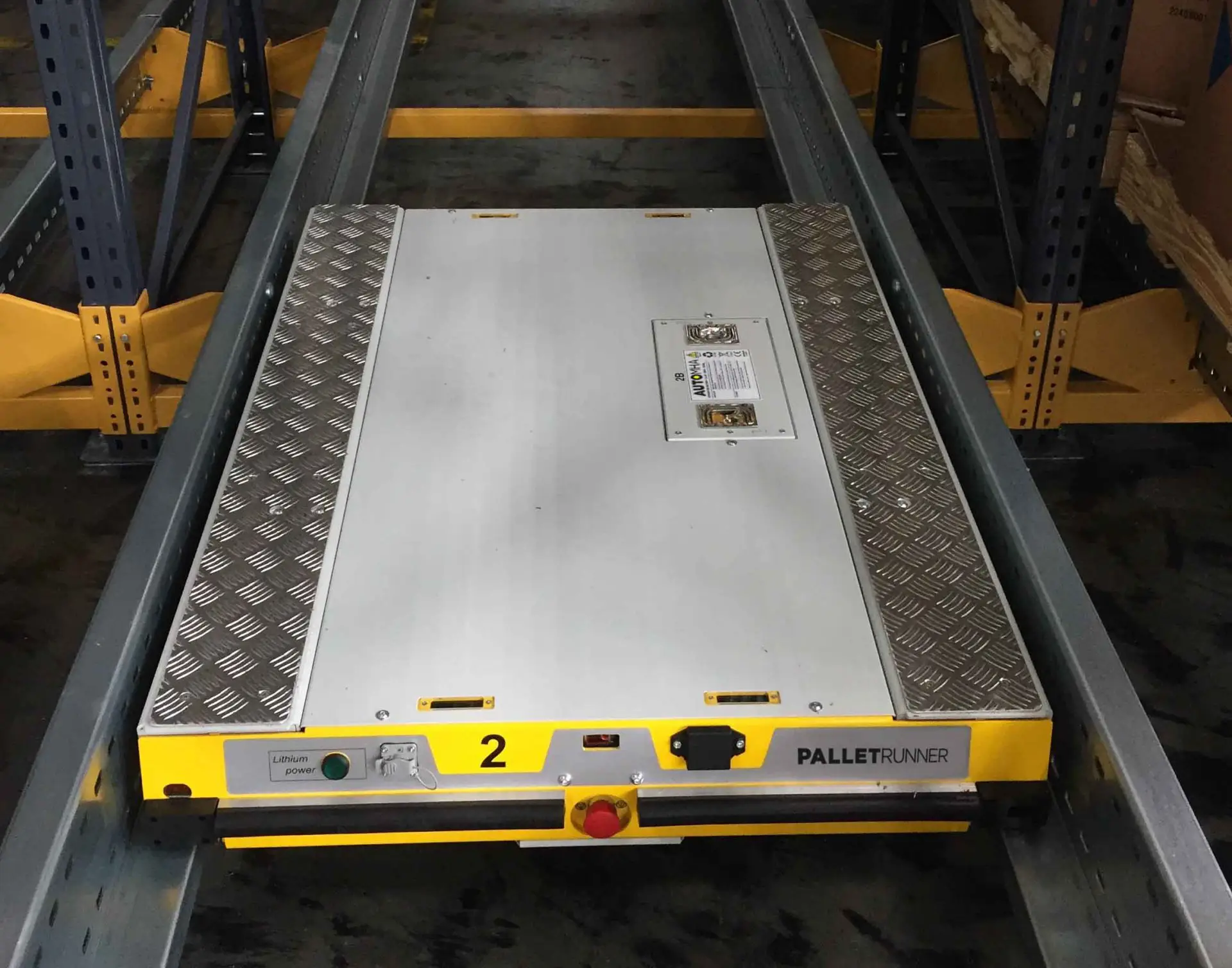
Key Benefits of Pallet Shuttle Systems:
- High Density: Maximizes storage space by utilizing deep lane storage, reducing the number of aisles needed and allowing for more pallets to be stored in the same footprint.
- Automation: Enhances efficiency through automation, minimizing manual labor and reducing the risk of human error. The automated shuttle can handle repetitive tasks, allowing warehouse staff to focus on more complex operations.
- Speed and Accuracy: Increases the speed and accuracy of loading and unloading pallets, improving overall productivity and reducing lead times.
- Versatility: Can be used in both FIFO (First-In-First-Out) and LIFO (Last-In-First-Out) configurations, making it adaptable to various inventory management strategies.
- Safety: Reduces the need for forklifts to enter the racking system, minimizing the risk of accidents and enhancing workplace safety.
What Is The Best Pallet Racking Solution For Your Business?
Choosing the right pallet racking system depends on various factors including the type of product stored, inventory management requirements, available warehouse space, and material handling equipment availability. By understanding the benefits and applications of each type of pallet racking system, you can make an informed decision that optimizes your warehouse storage and improves overall efficiency.
At Prestige, we specialize in providing tailored storage solutions to meet your specific needs. Our expertise in pallet racking systems ensures that you receive the best possible solution for your warehouse. Contact us today to learn more about our pallet racking systems and how we can help you optimize your warehouse operations.